川崎「ロボットテックミートアップ」で東京ロボティクス、クボタ、GBSの3社が講演
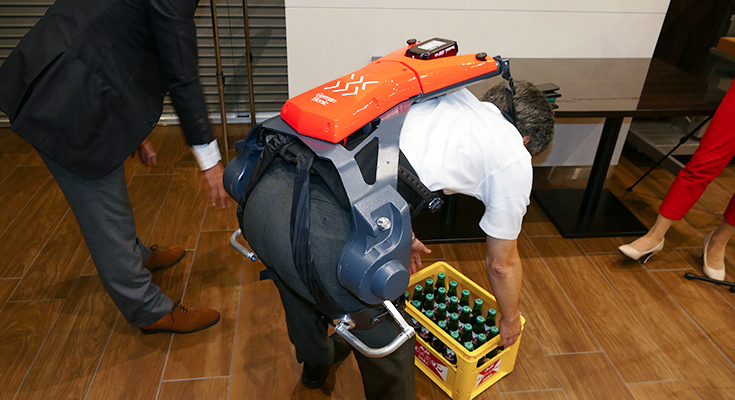
かわさき新産業創造センターの産学交流・研究開発施設「AIRBIC(エアビック)」で、2019年9月12日、ロボット分野にフォーカスした技術者の交流会「ロボットテックミートアップ Vol.3」が行われた。東京ロボティクス株式会社、株式会社クボタ、GBS株式会社の3社がプレゼンを行った。
開会に先立ち、主催者である、かわさき新産業創造センター所長の渡邉幹夫氏は「Robot Tech Meetupは毎回好評いただいている。先進的企業の話題を聞いた上で意見交換をして交流を深め、交流が連携につながっていくことを望んでいる」と語った。各社のプレゼンをレポートする。
・力制御と画像認識「Torobo Arm」の東京ロボティクス
・直進アシストで一人での作業が可能に、有人機と無人機の協調作業 クボタのロボット農機
・コネクテッド・エクソスケルトン「Cray X」のGBS
力制御と画像認識「Torobo Arm」の東京ロボティクス
まずはじめに、東京ロボティクス株式会社代表取締役の坂本義弘氏が「人間共存ロボットの実用化を目指して」と題して講演した。東京ロボティクスは早稲田大学 菅野研究室発のベンチャーで、2015年1月創業。柔軟関節ロボットアームの実用化を目指している。坂本氏は「産業用ロボットの流れは10年、15年スパンで決まっている」と見ているという。既存の産業用ロボットは協働ロボットを経て、今後は力制御するようになり、さらに移動ロボットと一体となって移動マニピュレータとなって、サービスなど様々な分野に入っていくだろうというのが坂本氏の見立てだ。
そして同社は「半歩先を行くロボットを作っている」と述べて、「Torobo Arm」シリーズを紹介した。これまでに30機関に40台を販売している。同社のロボットは関節をフレームレスモーターやモータードライバーなど部品単位で購入して内製化しており、特にコンパクトな関節の実現に強みを持っている。コントローラーも小型化しており、弁当箱サイズとなっている。ただし安全モジュールなどを入れると大きくならざるを得ないが、それでもカバンサイズにはしたいという。
DC24Vと低電圧で駆動するところも強みで、バッテリー駆動できる。そのためモバイルマニピュレータにも用いられている。四年半かけてロボットの基礎技術をだいぶ高めたと自負しているという。そこで今後はアプリケーションだということで、センシングや機械学習を使った画像認識などにも力を入れつつある。
「Torobo」シリーズは外力に追従し、あたかもバネとダンパーが入っているかのような動きをソフトウェアで実現している。ソフトウェアなので関節の柔らかさを任意に変えられる。また、ロボットが2点間を行ったり来たり動作中に人間が邪魔をしてもタスクを継続できる。これは通常の産業用ロボットでは実現できない動きだ。東京ロボティクスでは、これらの技術を組み合わせた上体型のヒューマノイドを作り、研究開発用プラットフォームとして提供している。
関節の柔軟性はドア開けや引き出し開けのように、環境との積極的な接触とある程度曖昧な動作計画が必要な作業に適用できる。関節の硬さはソフトウェアで任意に変えられるので動きも作りやすいという。産業用途ではバフがけ、バリ取り、コネクタ差し込み検査などが考えられる。関節トルクセンサを使っているので外力応答も敏感にできる、つまり接触すればすぐに止められる安全性があると坂本氏はアピールした。
センシングについては野菜のような不定形物のハンドリングを行なっている。野菜は工場で作る部品と違ってテンプレートマッチングができないのでディープラーニングを活用して物体を認識、掴む場所を判定して、しかるべき場所に置くような作業ができる。およそ9割程度の精度だという。
ただしアノテーションデータの作成は大変だ。そこで学習データの自動生成の研究も進めている。一週間人力でやっていたのものが1日で自動生成できるようになっているという。
紐や洗濯物など柔軟物のハンドリングもRNN(再帰型ニューラルネットワーク)を使って行なっている。ただしまだ成功率は半分くらいで未成熟だという。
早稲田大学とは自動解体のためのネジ検出の研究を行なっていた。様々な電子基板の画像からネジの位置をCNNを使って発見することができる。現在、人材を増強しており、技術ポートフォリオを増やしたいと考えているという。
坂本氏が今回繰り返し強調していたのが「アプリケーションを持っている現場の人たちと実証実験を進めていきたい」ということだった。従来の産業用ロボットはティーチングペンダントを使って繰り返し動作を教えていた。しかしこれでは教えた動作しかできない。坂本氏らは、今後はロボット自身が見て考えて動く自律化が進むのが必然的な流れだと考えて、研究開発を進めている。
また、今のロボットシステムはロボット本体の価格だけでなく、その5倍から10倍のシステム化コストがかかる。そのため大勢の人を代替できるシステムでないと自動化を進めるメリットがなかった。だが人を代替するロボットができれば、もっと自動化が進み幅広く使われるようになると考えて、いま同社では移動マニピュレータを使ってライン出入り口作業の自動化を行おうとメーカーと検証中だ。なおメーカーと検証を進めるときも技術は自社で持つようにしているという。
また、縫製作業の自動化も進めている。いま多くが海外で行われている縫製作業だが、海外の人件費も上がりつつある。数年後には日本国内に戻すことになるのではないかという考えのメーカーと、布地を折りたたむ作業から、いま基礎研究を進めている段階だという。
ロボットの遠隔操作も行なっている。NTTコミュニケーションズと共同でテレイグジスタンス事業を進めている。今年11月までのプロジェクトで、世界でトップクラスの遠隔操作ロボットを作ろうとしているという。具体的にはデータセンターの遠隔保守をやろうとしている。ラックを開け、コンソールケーブルを挿し、ロボットを介して遠隔保守をするという想定だ。
基本的にはどの取り組みもアプリケーションを持っている企業とやりたいと考えて各種PoCを進めているという。コストとニーズの強さを考えると「危険作業系がメインのフィールドになるのではないかと考えている」と坂本氏は述べた。
提案して実現に至ってないものとしては食品・食材のハンドリングがある。これについてはユーザーを募集しており提案して回っているところだという。
また実験自動化についても同じくパートナー募集中であり、実際に分注ロボットは試作したとのこと。
力制御と画像処理を中心にロボット関連技術のポートフォリオを継続的に強化しているとまとめた。現時点では研究開発が東京ロボティクスの主なビジネス領域となっているが、将来的にはロボット売りっぱなしではなくRaaSを想定してビジネスを進めていきたいという。
直進アシストで一人での作業が可能に、有人機と無人機の協調作業 クボタのロボット農機
続けて、株式会社クボタイノベーションセンターの千葉翔太氏が同社のロボット農機への取り組みについて紹介した。千葉氏は、これまで油圧バルブの研究開発に携わっていたが、2019年6月のイノベーションセンター設立を機に異動し、現在はベンチャー企業や大学とのオープンイノベーションによる新規事業企画・立案に従事しているとのこと。
クボタは2018年12月期の売り上げ高がおよそ1兆8500億円。事業別では機械事業が伸びている。日本では農業就労者が高齢化、離農により大幅に減少している。いっぽう、5ha以上の「担い手農家」が増えている。担い手農家の課題は分散した多数の圃場管理、生産コスト削減、生産品の高負荷価値化や人材育成、販路拡大などがある。これらを解決する手段としてデータ活用に精密農業の導入が進められつつある。
クボタもそのニーズに応えて、高性能・高耐久農機の販売や、営農ソリューションの提案、スマート農機ん開発を進めている。農業機器は機械化をへて、今ではデータ活用による精密農業と、自動運転農機による超省力化が進められようとしている。
たとえばクボタは稲作のそれぞれの段階に対してソリューションを提案している。データを見える化できる営農支援システム「KSAS」で経営を管理し、田植えを直進運転でサポートすることで初心者でも熟練者並に田植え機を操作できるようにしている。水管理・草刈についても給排水の自動制御、ラジコン草刈機による除草の軽労化を進め、防除・追肥についてはドローン活用、リモートセンシングが進めらている。収穫はコンバインに食味センサーがついており、データ収集と栽培アドバイスも行えるようになっている。一貫体系となっている点が特徴だ。
無人農機は、直進サポートのオートステアがレベル1、有人監視での自動化・無人化がレベル2、そして完全無人化がレベル3とされている。千葉氏はクボタのラインナップを紹介した。
2016年秋にリリースされた直進キープ機能つき田植え機は、比較的安価なD-GPSアンテナとIMUを組み合わせた独自の直進制御プログラムにより、100m直進で誤差が10cm以内の精度で、簡単にまっすぐ田植えができる機能を実現した。これによって作業ストレスが軽減できる。また、植え付け中に施肥の確認ができ効率があがる。特に、一人で作業ができるようになった点が評価が高いという。田植え機に予め搭載した予備苗を順次補充しながら運転する必要があるため以前は二人で乗り込んで分担するのが当たり前だったが、アシストのおかげで直進している間に人が補充をすることで、一人だけで連続作業ができるようになった。最初に基準となるラインを運転する必要はあるが、そのあとは、そのラインに平行になるように走行をアシストする。これによって直進時の手放し運転を実現した。
直進機能付きの小型トラクタも2019年の1月からリリースしている。ハンドル操作自体は田んぼのほうが難しいが、畑は斜面の影響があり、そこが技術的ハードルだったという。
レベル2(有人監視下の自動運転)へは、アグリロボコンバインを2018年12月から販売し、同トラクタは現在モニター販売中。自動運転田植え機は近いうちに製品化されるレベルにあるという。
耕運と代かき作業を行うアグリロボトラクタは高精度なRTK-GPSを用いて2台の協調運転が可能だ。一台が有人、もう一台が無人という形でトラクタを自動運転するので、作業者一人で二台を運用できる。まず最初に圃場の外形を走行させてマッピングし、それをもとに自動運転を行う。四角い圃場でなくても対応可能だ。障害物検知にはレーザーや超音波ソナーなど複数のセンサーを用いている。千葉氏は有人機と無人機の協調作業の様子を示した。
自動運転アシスト機能つきコンバインは、作業時間が最短になるように人間ができないルート取りができるところが一番の特徴だ。人間が刈り取り運転をやると基本的には順番にやっていくしかないが、機械は、一番最適に車が回れるように効率的に計算ができる。そのため、いったん間を飛ばすようなルート取りをすることもできるのだという。
完全無人化については農研機構や大学と研究を進めている。レベル2における課題としては、無人化のための圃場基盤の整備と圃場全域の無人化、安全対策の高度化、適応作業の拡大、準天頂衛星による測位システムの低コスト化を挙げた。コンバインは稲を刈り取るので単純に障害物を認識したら止まるといったことはできないところが難しい。
レベル3の課題については、遠隔監視のための圃場基盤・農道の整備、5Gや通信規制の緩和、3Dダイナミックマップの活用など道路走行技術の構築、トラクタのインプルメント装着状態での走行など道路交通法の緩和などを挙げた。会場からは電動化についての質問も出たが、農機はパワーが必要であり、どうしてもバッテリーだけでは難しいと述べた。
コネクテッド・エクソスケルトン「Cray X」のGBS
最後に、GBS株式会社の代表取締役社長の山下英夫氏が「インダストリー向けエクソスケルトン/パワースーツCray X」と題して講演した。同社の「Cray X」は身体に装着することで重量物持ち上げ時の腰の負荷を下げるパワースーツ。GBSでは「世界初のコネクテッド・エクソスケルトン」としており、IoT対応である点が特徴となっている。
Cray Xは身体の動きを検出して腰部分のアクチュエータを駆動して最大20kgまでのサポートを行う。本体の重量は約8kg。バッテリー動作時間は8時間。
主な用途は産業用だ。厚生労働省の基準によれば、人が運んでいも良い最大重量は55kgとされている。たとえば電線の一巻きが50kgだそうだ。こういったものや、組み立て家具の運搬作業などが同社のスーツのユースケースである。特に強いアシスト力が売りだという。
ドイツに本社があるGerman Bionic Systems(GBS)は、ドイツでは唯一のエクソスケルトン開発メーカー。同社のエクソスケルトンは、もともとは「RoboMate」というEUの研究プロジェクトが元となっている。同社創業者のピーター・ハイリンセッツァー氏は「産業界最大の発明はメガネだ(メガネによって、視力が悪い人も働ける職業が増えた)」と言っているそうで、エクソスケルトンがメガネのように広く使われることを目指しているという。開発陣の多くはKUKA出身だ。GBS株式会社はその日本法人で銀座オフィスと新川崎に拠点を置いている。
山下氏は、今後はアクティブ型のアシストスーツの市場が大きくなると言われていると紹介し、特にヨーロッパ、アジア市場が伸びると考えていると語った。対象分野としては物流や工場、そしてホームセンターなどでの活用が考えられている。
製品ラインナップは2種類。「Cray X」は産業用のエクソスケルトンである。「Cray +」はまだ出荷に至っていないが、レスキュー向けの、よりパワーの大きいエクソスケルトンだ。前述のとおり、他の競合製品に比べて出力がはるかに大きく、物理的に腰を守るストラクチャーがある点が売りだという。大きな出力にも耐えられる耐久性もある。ドイツではいまエクソスケルトン専用工場を作り、量産を進めようとしている段階だ。外科医との共同研究も進めていて、身体の負荷をどのように低減しているのかも研究中だという。
もとがドイツの会社なのでヨーロッパを中心としているが、アジアでは日本を拠点とし、韓国やシンガポール、マレーシア、香港などに販売を広げていく。ドイツ・ドルトムントではIKEAロジステティクスでも2019年7月中旬から使われている。
日本国内でも主に製造業現場での活用を考えているが、ラインのように継続的な業務が続く作業ではなく、部品の搬入や積み込みなどでの活用を考えているという。建設業においても、建設作業そのものではなく、主に搬入作業などでの活用を想定している。同社が市場に出すまでは想定していなかったユーザー層としては、製薬メーカーでの原料粉末の運搬などに用いられている例や、クリーンスーツをロボット装着の上で来て活用している例などがある。
「Cray X」最大の特徴が「German Bionic IO」である。通信機能を持つエクソスケルトン・スーツからセンサーデータを取ることで、いつどこで誰がどんな作業をやったのかといったことを20数種類のセンサデータから取得することができる。これによって「人間系のブラックボックス」を見える化することができる。外部からソフトウェアアップデートも可能だ。
サービスの柔軟性を上げ、ユーザーの導入ハードルを下げるためにRasSサービスも始めている。初期費用は649,000円で、月額124,000円から使ってもらうというプランだ。山下氏は最後に「様々な現場で使えることを知ってもらいたい。広くユーザーストーリーを提供していきたい」と語って講演を締めくくった。
ABOUT THE AUTHOR /
森山 和道
フリーランスのサイエンスライター。1970年生。愛媛県宇和島市出身。1993年に広島大学理学部地質学科卒業。同年、NHKにディレクターとして入局。教育番組、芸能系生放送番組、ポップな科学番組等の制作に従事する。1997年8月末日退職。フリーライターになる。現在、科学技術分野全般を対象に取材執筆を行う。特に脳科学、ロボティクス、インターフェースデザイン分野。研究者インタビューを得意とする。WEB:http://moriyama.com/ Twitter:https://twitter.com/kmoriyama 著書:ロボットパークは大さわぎ! (学研まんが科学ふしぎクエスト)が好評発売中!